In the relentless march toward Industry 4.0, data integration in manufacturing stands as the linchpin of modern industrial operations. Data integration delivers a cohesive and panoramic view of manufacturing operations by merging and managing data from diverse sources such as equipment, supply chains, and customer feedback systems. This synthesis of information enables manufacturers to analyze and leverage data with unprecedented efficacy, driving precision, speed, and strategic agility.
DATAFOREST knows the nine must-have integrations redefining the manufacturing sector. From ERP systems that bridge departmental silos to IoT integrations that enable predictive maintenance, we explore how data integration in manufacturing is revolutionizing operations, enhancing productivity, and fostering innovation.
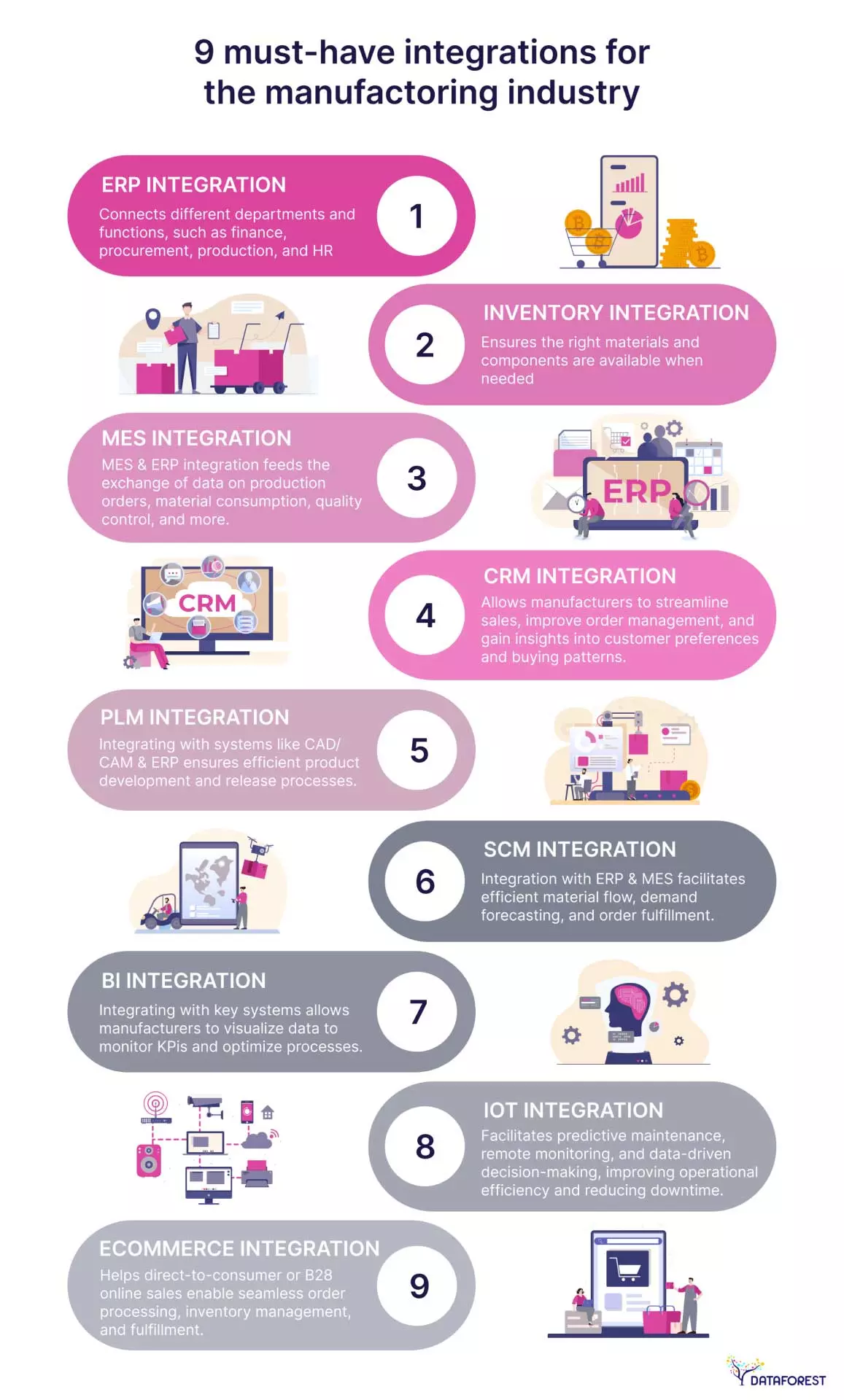
Must-Have Integrations for the Manufacturing Industry
- ERP Integration: Enterprise Resource Planning (ERP) integration is crucial for connecting various departments and functions within a manufacturing organization, such as finance, procurement, production, and HR. This integration ensures a unified data flow, enabling comprehensive visibility and control over business processes.
- Inventory Integration: Effective inventory management is vital for manufacturing success. Inventory integration ensures that suitable materials and components are available when needed, automates reordering, and minimizes stockouts and overstock situations. This integration is critical to optimizing the supply chain and maintaining production continuity.
- MES Integration: Manufacturing Execution Systems (MES) integration with ERP systems facilitates data exchange on production orders, material consumption, quality control, and more. This real-time data exchange enhances production efficiency, reduces waste, and ensures that manufacturing operations align with business goals.
- CRM Integration: Customer Relationship Management (CRM) integration allows manufacturers to streamline sales, improve order management, and gain insights into customer preferences and buying patterns. This integration helps build stronger customer relationships and tailor products and services to meet market demands.
- PLM Integration: Product Lifecycle Management (PLM) integration with systems like CAD/CAM and ERP ensures efficient product development and release processes. By integrating PLM, manufacturers can manage product data, streamline engineering changes, and accelerate time-to-market.
- SCM Integration: Supply Chain Management (SCM) integration with ERP and MES systems facilitates efficient material flow, demand forecasting, and order fulfillment. This integration optimizes the supply chain, reduces lead times, and enhances overall agility.
- BI Integration: Business Intelligence (BI) integration with critical systems allows manufacturers to visualize data, monitor key performance indicators (KPIs), and optimize processes. Manufacturers can make data-driven decisions, identify trends, and improve operational efficiency by integrating BI tools.
- IoT Integration: The Internet of Things (IoT) integration enables predictive maintenance, remote monitoring, and data-driven decision-making. By incorporating IoT, manufacturers can enhance operational efficiency, reduce downtime, and implement proactive maintenance strategies.
- Ecommerce Integration: Ecommerce integration supports direct-to-consumer or B2B online sales, enabling seamless order processing, inventory management, and fulfillment. This integration is essential for manufacturers looking to expand their market reach and provide a superior customer experience.
Data integration in manufacturing is a game-changer, offering a strategic advantage to manufacturers who embrace it. These nine integrations are essential for driving efficiency, agility, and innovation in the manufacturing sector.
Our subject matter experts' article will explore the multifaceted benefits and practical applications of data integration in manufacturing in this article. We will delve into its pivotal role in enhancing decision-making, improving product quality, boosting operational efficiency, reducing costs, and implementing predictive maintenance strategies.
We will also examine paramount technologies and techniques, address common challenges, and highlight real-world case studies to illustrate the transformative impact of data integration in the manufacturing sector.
What is Data Integration in Manufacturing, and Why It’s Essential?
Data integration in manufacturing is merging and managing data from various sources within the manufacturing ecosystem, including equipment, supply chains, and customer feedback systems. This integration delivers a cohesive view of operations, enabling manufacturers to analyze and utilize information more effectively. Robust data integration is indispensable in today's fast-paced manufacturing environment, where precision and speed are crucial. It underpins real-time decision-making and strategic planning, ensuring manufacturers can swiftly adapt to market changes and operational demands.
How Data Integration Empowers Manufacturers
Effective data integration in manufacturing unlocks the full potential of informational assets, enhancing analytics, improving forecasting, and boosting process automation. For instance, integrated data systems can predict equipment maintenance needs before breakdowns occur, reducing downtime and extending the lifespan of valuable assets. This empowerment provides greater control over operations and instills confidence in decision-making.
Additionally, advanced data integration offers insights into customer behaviors, facilitating targeted marketing and product development strategies. Ultimately, data integration in manufacturing is a powerful tool that drives efficiency, supports sustainable practices and fosters innovation within the industrial sector. By embracing data integration, manufacturers can improve operations and contribute to a more sustainable and innovative future for the industry.
Types of Data in Manufacturing
Understanding Various Data Types in Manufacturing
Manufacturing operations generate a vast array of data types, each offering crucial insights into different aspects of production.
- Process Data: Information about manufacturing operations, such as temperatures, speeds, and feed rates, is essential for evaluating the efficiency and effectiveness of production techniques.
- Quality Data: Metrics and measurements related to the standards and specifications of finished products are vital for ensuring customer satisfaction and regulatory compliance.
- Equipment Data: Details about the performance and status of machinery and tools, such as usage rates, fault logs, and maintenance records, are critical for ensuring operational reliability and longevity.
The Benefits of Integrating Diverse Data Types
Integrating diverse data types within a manufacturing setting provides a comprehensive view of operations. Manufacturers gain a multidimensional perspective that enhances informed decision-making by merging process, quality, and equipment data.
For example, correlating process data with quality outcomes can identify specific production steps directly impacting product standards. Similarly, integrating equipment data with process information can optimize machine usage, leading to better maintenance schedules and reduced downtime. This comprehensive data integration facilitates real-time decision-making and strategic long-term planning, aligning all aspects of manufacturing with business objectives. This multi-layered approach to data utilization boosts efficiency, drives innovation, and significantly enhances competitiveness in the manufacturing sector.
Benefits of Data Integration in Manufacturing
Enhanced Decision-Making with Comprehensive Data Integration
One of the paramount advantages of data integration in manufacturing is the profound enhancement of decision-making processes. Access to integrated data provides decision-makers with comprehensive, accurate, and real-time information, enabling swift and effective responses to opportunities and challenges. Whether it's strategic decisions like expansion plans or operational adjustments based on market demands, integrated data offers a holistic view of the manufacturing landscape. This integration significantly reduces risks, fostering more confident, informed choices and ensuring businesses stay ahead of the curve.
Improved Product Quality through Continuous Monitoring
Data integration in manufacturing processes allows continuous monitoring and stringent product quality control. Manufacturers can significantly enhance product outputs by analyzing quality data alongside process and equipment data. For instance, integrated data can reveal correlations between production conditions and defect occurrences, enabling fine-tuning processes to preempt quality issues before products reach the customer. This proactive quality assurance approach maintains high standards and boosts customer satisfaction by delivering consistently superior products.
Boosting Operational Efficiency with Unified Data Environments
A unified data environment is crucial for boosting manufacturing operational efficiency. Manufacturers can streamline processes, reduce redundancy, and optimize workflows by integrating data. Data-driven insights refine production schedules, manage inventory more effectively, and improve resource allocation. These enhancements speed up operations and increase the agility and flexibility of manufacturing systems, enabling them to adapt swiftly to transforming market conditions or customer requirements.
Check out our data integration services for detailed strategies for boosting operational efficiency.
Significant Cost Reduction through Efficient Data Handling
Integrating data in manufacturing leads to significant cost reductions by identifying and eliminating wasteful practices, reducing energy usage, minimizing raw material wastage, and optimizing supply chain operations. For instance, integrated data systems can pinpoint inefficiencies in energy consumption or highlight excessive downtime linked to specific production lines, providing clear targets for cost-saving measures. These operational cost reductions directly improve the bottom line, making businesses more competitive and sustainable.
Predictive Maintenance: Prolonging Equipment Life and Reducing Costs
Manufacturing data integration is instrumental in facilitating predictive maintenance. By analyzing equipment data over time, predictive models can forecast potential failures before they occur, allowing for timely maintenance interventions. This approach minimizes unplanned downtime, extends machinery life, and reduces maintenance costs. Predictive maintenance ensures equipment operates at peak efficiency, supporting a predictable and reliable production schedule crucial for meeting customer demands and maintaining production quality.
Manufacturing data integration is a game-changer for the industrial sector, offering myriad benefits from improved decision-making to enhanced product quality, increased operational efficiency, significant cost reductions, and the implementation of predictive maintenance strategies. By leveraging integrated data, manufacturers can drive innovation, maintain high standards, and stay competitive in a rapidly evolving market. Embracing manufacturing data integration is not just a technological upgrade; it's a strategic imperative for any forward-thinking industrial business.
Key Data Integration Technologies and Techniques
ETL (Extract, Transform, Load) Processes: Preparing Data for Integration
ETL processes are fundamental in manufacturing data integration, especially in complex environments where data must be consolidated from multiple sources.
- Extract: This phase collects data from diverse origins, including on-premise databases, cloud storage, and direct manufacturing equipment.
- Transform: Data is cleansed, formatted, and normalized to ensure consistency. This involves sorting, summarizing, and applying computational functions.
- Load: The processed data is transferred into a central repository, such as a data warehouse, ensuring accuracy and readiness for integration.
APIs (Application Programming Interfaces): Enabling Communication Between Systems
APIs are essential for modern manufacturing data integration, serving as intermediaries that facilitate seamless communication between disparate systems. APIs reduce complexity and enable scalable integration solutions by standardizing interactions between applications. This flexibility allows manufacturers to connect CRM software with production management systems and enable real-time data feeds from IoT devices, enhancing adaptability to new technologies and business needs.
Data Warehousing: Centralizing Data for Integration
Data warehousing centralizes data from various sources, providing a comprehensive repository for analysis. In manufacturing, data warehouses aggregate historical and real-time data across the production lifecycle, from supply chain details to customer feedback. This centralized approach supports advanced data mining and business intelligence tools, uncovering patterns and insights that enhance decision-making and operational efficiency.
IoT (Internet of Things) Devices: Collecting and Transmitting Data from the Manufacturing Floor
IoT devices revolutionize data integration by offering continuous real-time data streams directly from the manufacturing floor. These devices, ranging from sensors on equipment to RFID tags on products, collect diverse data, including temperature, pressure, speed, and output rates. This data is transmitted wirelessly to central systems or the cloud for immediate integration and analysis, enabling precise monitoring and rapid response to emerging issues, thus boosting efficiency and productivity.
Big Data and Analytics: Extracting Value from Integrated Data
Big data technologies are crucial for processing and analyzing large, complex datasets generated by integrated systems in manufacturing. Advanced analytics enable manufacturers to discover trends, predict outcomes, and generate actionable insights. This can lead to more precise demand forecasting, enhanced product customization, and optimized production processes, transforming integrated data into a strategic asset for more intelligent business decisions.
Data Security and Privacy in Manufacturing Data Integration
Importance of Data Security and Privacy in Manufacturing
Security and privacy are paramount in manufacturing, where data integration involves handling sensitive information ranging from proprietary production techniques to personal employee data.
The integration process often exposes data to additional vulnerabilities as it transitions between systems or is accessed by various stakeholders. Ensuring this data's confidentiality, integrity, and availability is crucial for maintaining a competitive advantage and complying with legal and ethical standards.
Manufacturers must prioritize robust security benchmarks to safeguard against data breaches, unauthorized access, and other cyber threats, which can have severe financial and reputational repercussions.
Best Practices and Compliance Considerations
Best practices in data security for manufacturing data integration include implementing strong access controls, encrypting data at rest and in transit, and regularly auditing data usage and security protocols.
Moreover, compliance with regulations like the General Data Protection Regulation (GDPR) in the EU or industry-specific guidelines like those from the National Institute of Standards and Technology (NIST) in the U.S. is essential.
These regulations often require strict data handling procedures and can dictate how data should be collected, stored, processed, and shared. Adherence to these regulations helps avoid hefty fines and creates trust with clients and partners by demonstrating a commitment to data protection.
Challenges and Considerations
Common Challenges in Manufacturing Data Integration
Despite its benefits, manufacturing data integration presents significant challenges.
Data silos, where data is isolated within different departments or systems, can impede the free flow of data, making effective integration difficult. Overcoming these silos requires not only technical solutions but also organizational change management.
Another common hurdle is compatibility issues, which can arise from disparate systems operating on different technology platforms. These issues require specialized middleware or extensive modifications to ensure seamless integration.
Additionally, data quality issues, such as incorrect, incomplete, or unreliable data, can severely impact the effectiveness of data integration efforts. Addressing these challenges requires a concerted effort toward standardization, rigorous data governance policies, and ongoing monitoring and maintenance of the data integration infrastructure.
The Evolution and Impact of Data Integration in Manufacturing
Key Trends in 2025
- Smart Factories: The idea of smart factories is at the forefront of data integration in manufacturing. Utilizing advanced technologies such as SCADA systems, 5G, IIOT, machine learning, and robotics, these factories enable real-time data collection and analysis. This integration optimizes operations, enhances supply chain resilience, and significantly boosts asset efficiency, labor productivity, and product quality, all while reducing operational costs. According to Deloitte, smart factories represent a revolutionary step in manufacturing.
- Microfactories: Microfactories embody flexibility, customization, and localization, making them a pivotal element in the landscape of data integration in manufacturing. These agile, smaller-scale factories incorporate innovative features to improve efficiency and responsiveness to market demands.
- Giga Casting: Giga casting is revolutionizing the automotive sector by producing large car parts in a single cast, thus reducing weight, cost, and complexity. Industry leaders like Tesla, Toyota, and Volvo are pioneering this technology to enhance the performance and efficiency of electric vehicles.
- Predictive Analytics and Machine Learning: Integrating AI and machine learning is essential for analyzing vast datasets in manufacturing. These technologies identify patterns and predict equipment failures, significantly contributing to data integration in manufacturing.
In 2025, data integration in manufacturing will be driven by smart factories, micro-factories, and sophisticated data analytics. These trends, supported by scientific advancements, are reshaping the industry by enhancing efficiency, reducing costs, and improving product quality. As manufacturers embrace these technologies, the future of manufacturing will become increasingly innovative and efficient.
Real-World Examples and Case Studies of Data Integration in Manufacturing
Siemens
Siemens exemplifies data integration in manufacturing by using AI for predictive maintenance, quality control, and energy efficiency. By analyzing data from machinery sensors, Siemens predicts equipment failures before they happen, reducing unplanned downtime. AI-powered visual inspection systems automate quality control, ensuring high product standards. These advancements have saved millions of euros annually and cut energy consumption by 20%, aligning with Siemens' sustainability goals.
General Electric (GE)
GE's Predix platform, a cloud-based PaaS, enhances data integration in manufacturing by improving power plant efficiency. Digital twins and advanced analytics drive operational improvements, leading to a 40% reduction in unexpected downtime and a 20% decrease in maintenance costs. Optimizing fuel consumption has also improved output by 10%, highlighting GE's successful integration of AI and machine learning technologies.
Toyota Motor Corporation
Toyota integrates data through AI and robotics to refine its manufacturing processes. Advanced robotics enhance production line precision and efficiency, while AI-powered visual inspections reduce defects by 30%. Furthermore, AI-driven supply chain optimization cuts inventory costs by 20%, and energy management systems lower energy consumption by 15%, supporting Toyota's sustainability objectives.
Procter & Gamble (P&G)
P&G leverages Microsoft Azure for data integration across over 100 manufacturing sites globally. This digital transformation enhances AI, ML, and edge computing capabilities, optimizing production processes and improving operational efficiency. Data integration enables better decision-making and streamlined operations across P&G's global facilities.
IoT in Manufacturing
The integration of IoT in manufacturing presents numerous opportunities for operational improvement. Remote equipment monitoring through IoT sensors allows manufacturers to assess performance and deploy services as needed, enhancing product design and customer satisfaction. Real-time machine monitoring provides immediate data for decision-making, ensuring production schedules are met. Predictive maintenance, facilitated by IoT-connected equipment, transitions manufacturers from calendar-based to condition-based maintenance strategies, significantly reducing downtime and maintenance costs.
These case studies highlight the transformative impact of data integration in manufacturing. By leveraging advanced technologies like AI, ML, and IoT, companies achieve substantial gains in efficiency, cost reduction, and product quality, establishing themselves as leaders in the digital transformation of manufacturing.
Practical Insights for Effective Data Integration by DATAFOREST
Integrating data in manufacturing is a strategic imperative that can drive operational efficiency, enhance product quality, and enable predictive maintenance. By leveraging advanced technologies and best practices, manufacturers can harness the power of integrated data to make informed decisions, optimize processes, and stay competitive in a dynamic market. Explore more about data integration techniques and how to revolutionize data integration in marketing with DATAFOREST's comprehensive manuals.
Manufacturing data integration is a powerful catalyst for industry transformation. It enables enhanced decision-making, operational efficiency, and more robust security practices.
However, realizing these benefits requires navigating a complex landscape of technical challenges and regulatory requirements.
By understanding the types of data involved, leveraging the right technologies and techniques, and prioritizing data security, manufacturers can effectively integrate their data assets to drive innovation and hold a competitive edge in the market.
As technology evolves, staying ahead of these challenges and continuously adapting strategies will be vital to harnessing the full potential of data integration in manufacturing.
For further details and to explore case studies, visit DATAFOREST or contact us here.
Schedule a call with the DATAFOREST expert for a personal consultation.
FAQ
Is data integration relevant for areas other than production in manufacturing?
Manufacturing data integration is highly relevant beyond just production. It significantly enhances supply chain management by automating processes, improving efficiency, and increasing visibility across the manufacturing process. This comprehensive data integration in manufacturing ensures real-time responsiveness, enabling manufacturers to adapt quickly to changes and demands, optimizing the supply chain, and improving customer satisfaction.
Are there specific regulations that manufacturers need to follow when integrating data?
Manufacturers must adhere to industry-specific standards and general regulations when implementing manufacturing data integration. For instance, ISO 9001 is crucial for maintaining quality management systems, while GDPR protects personal data. Adherence with these regulations is essential to secure data integrity and avoid legal repercussions, making data integration in manufacturing a critical aspect of operational management.
Can small and medium-sized manufacturers benefit from data integration?
Small and medium-sized manufacturers can significantly benefit from manufacturing data integration. Integrating data allows these manufacturers to streamline their operations, improving efficiency and reducing costs. Data integration in manufacturing empowers these businesses with enhanced decision-making capabilities, providing valuable insights into their processes. This fosters competitiveness and drives innovation, allowing smaller manufacturers to thrive in an increasingly data-driven industrial landscape.