Manufacturing under Energy 4.0 will feature fully automated smart factories with real-time energy monitoring and optimization at every production stage. AI-driven systems will dynamically adjust power consumption based on production demands, grid conditions, and energy prices. Digital twins will simulate and optimize energy usage throughout the manufacturing process, from raw material processing to final assembly. Renewable energy integration will be seamless, with smart microgrids balancing local generation and storage with grid power. The enterprise will operate as an interconnected system where every machine, process, and energy flow are monitored, analyzed, and optimized in real time for maximum performance and minimal environmental impact. DATAFOREST team will do the same in this and other industries; you need to arrange a call.
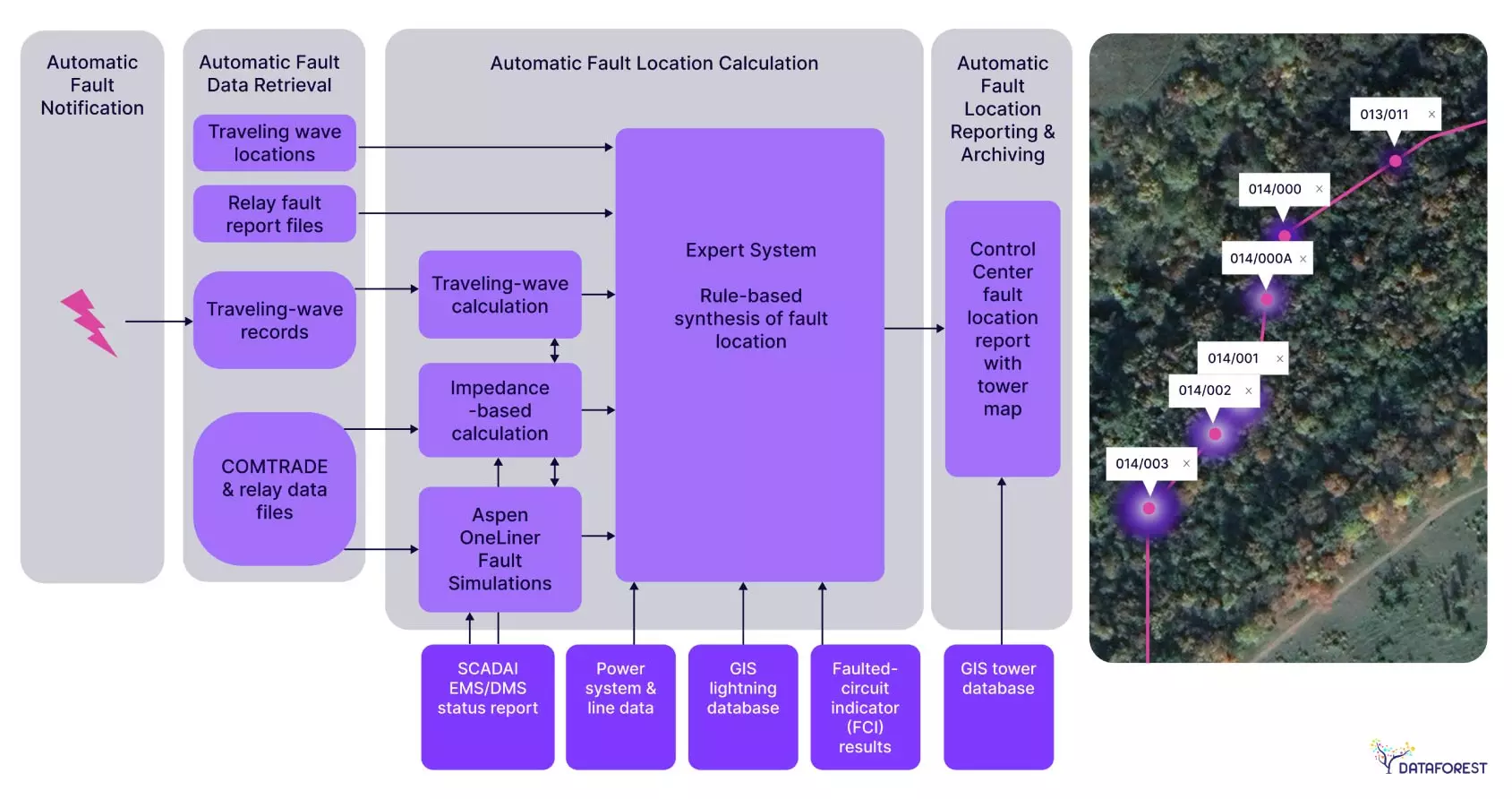
Energy 4.0 – Transforming Business Through Data-Driven Power Optimization
Energy 4.0 represents the grid modernization of the power generation sector through the integration of IoT devices, AI, big data energy analytics, and smart grid technology. Adopting energy forecasting and fault detection systems is crucial for businesses because they directly impact operational efficiency and the bottom line by reducing energy costs, minimizing downtime, and optimizing power plant operations.
Companies can analyze massive amounts of operational data to predict equipment failures, optimize maintenance schedules, and adjust data science for power generation through demand response based on forecasts. Meters and sensors provide insights into grid stability and energy consumption patterns to identify inefficiencies. This data-driven approach supports sustainability goals by enabling better integration of distributed energy resources, reducing waste, and lowering carbon emissions through optimized energy usage.
Powering the Future of Energy Management
Data science in power generation is changing the landscape through advanced energy forecasting, machine learning algorithms, and digital twin technology that processes big data from power plants, distribution networks, and end-user consumption points. This transformation enables predictive maintenance of equipment, reducing unexpected downtime and maintenance costs while extending asset life spans.
Real-time monitoring and AI-driven fault detection help identify inefficiencies, enabling adjustments that maximize power generation efficiency. IoT sensors provide granular data, allowing businesses to modify energy usage patterns and improve asset performance management. This transformation also addresses the intermittency challenges of renewable energy through energy storage systems.
Data science in power generation also manages intermittency challenges for renewable energy integration through accurate weather forecasting and demand prediction. Machine learning algorithms optimize the balance between conventional and renewable power sources, making sure reliable supply while minimizing costs and carbon emissions. This data-driven approach facilitates a smoother transition to sustainable energy while maintaining operational reliability.
How American and European Companies Can Leverage Energy 4.0
Using IoT sensors, companies can track energy use in real time and fine-tune it to save big. For instance, smart tech in factories has been shown to slash operating costs by up to 8.5%, which can mean $600 in savings per square foot yearly.
Cloud computing is another win. It moves hefty capital expenses to more flexible operational ones while offering scalable processing power and real-time analytics. This means fewer bottlenecks, better processes, and reduced waste.
Then there’s digital twin tech—virtual models of physical assets that let businesses predict maintenance issues before they cause expensive downtime. By integrating data science in power generation with digital twins, General Electric is already using over a million of these twins to keep its jet engines running smoother and longer.
Data Science Impacts Energy Infrastructure
Data science in power generation impacts energy infrastructure by analyzing massive amounts of real-time data from smart meters, sensors, and grid components to optimize power distribution and reduce waste. Machine learning algorithms enable predictive maintenance by identifying potential equipment failures before they occur, significantly reducing downtime and maintenance costs. Advanced analytics help integrate renewable energy sources more efficiently by forecasting production patterns and balancing supply with demand across the power grid.
Real-Time Energy Intelligence
Data science in power generation transforms energy management through three key layers: monitoring, analysis, and automated response. Smart meters and IoT sensors continuously collect usage data while algorithms process this information to detect real-time patterns and anomalies. The system then automatically adjusts energy distribution based on immediate needs, like a smart thermostat, but on a larger scale.
Small businesses can implement basic energy monitoring solutions, starting with simple meters and cloud-based analytics platforms. For example, a retail store can track hourly energy usage patterns, identifying peak consumption periods and unnecessary energy drains from equipment left running after hours. Most utility providers now offer innovative metering services with essential analytics tools at minimal additional cost, making this technology accessible to smaller operations.
Logistics Case Study
A medium-sized warehouse operation implemented essential energy monitoring in 2024:
Initial Investment: $3,500 for smart meters and basic analytics software
Implementation: Installed sensors on major equipment and lighting systems
Data Collection: Monitored energy usage patterns for 3 months
Key Findings
- 40% of energy was consumed during low-activity periods
- Lighting systems ran at full capacity regardless of occupancy
- Loading dock doors frequently left open, affecting climate control
Solutions Implemented
- Automated lighting based on occupancy and natural light levels
- Scheduled equipment power-down during inactive periods
- Door sensors with automatic alerts
Results
- 27% reduction in annual energy costs
- $42,000 savings in the first year
- ROI achieved within 4 months
- Additional savings from reduced equipment wear
This case demonstrates how even essential data-driven energy management can deliver significant returns without requiring extensive infrastructure changes or large capital investments.
A Competitive Energy Management Edge Through Data
Imagine having a data science in power generation system that knows exactly when and where you need power, making adjustments on the fly without you having to lift a finger.
With real-time monitoring and automated controls, you can spot energy waste instantly and fix it before it hits your wallet. The system watches for usage spikes, flags equipment not performing well, and adjusts to changing energy prices throughout the day.
The numbers tell the story – businesses using these innovative systems cut energy bills by 15-30%. But it's not just about saving money. You're also building a reputation as a forward-thinking company that cares about sustainability.
If you're not using data to manage your energy, you're basically flying blind. The market's moving fast, and customers are paying attention to how businesses handle their environmental impact. When new energy regulations come along (and they will), you'll already be ahead of the game. Smart energy management is nice to have anymore, and it's becoming a must-have for any business that wants to stay competitive.
Overcoming Challenges of Data Science in Power Generation
Common barriers to data science in power generation adoption stem primarily from aging infrastructure and legacy systems not designed for modern data collection and integration. There's often resistance from traditional power industry professionals who may lack data science expertise and concerns about cybersecurity when connecting critical power infrastructure to digital networks. The high initial costs of implementing data collection systems and regulatory uncertainties around grid security make organizations hesitant to embrace data science solutions.
Simplify Energy Data Integration for Smarter Power Generation
Start by centralizing data collection with IoT sensors across all energy sources—solar, wind, and traditional plants. Data science can be used in power generation tools like Apache Kafka or AWS Glue to unify data into a single system. Standardize communication with protocols like MQTT or OPC-UA for seamless device and system interactions. Build real-time data pipelines using tools like Apache Spark for live analytics' instant insights. Make sure your system supports advanced predictive maintenance and efficiency optimization. With these steps, you'll transform fragmented energy data into actionable insights, unlocking the full potential of your infrastructure.
Smarter Energy Management Across Sectors
Retail, fintech, and SaaS businesses are tackling energy integration issues by adopting data science in power generation tools and technologies.
If you think this is your case, then arrange a call.
Scalable Data Science Tools for AI-Driven Solutions
SMBs can harness AI without hefty investments by leveraging scalable data science tools. Platforms like Google Cloud AutoML, AWS SageMaker, and Microsoft Azure ML offer pay-as-you-go models. Open-source tools like TensorFlow and Scikit-learn enable affordable model building and deployment. Data integration platforms like Apache NiFi and cloud-based data lakes provide scalability as data grows. Pre-trained AI models and APIs like OpenAI or Hugging Face allow the implementation of advanced features without deep expertise. These tools democratize AI, empowering small businesses to optimize operations, personalize customer experiences, and make data-driven decisions affordably.
Scaling Data Science Solutions in Power Generation
Boost Equipment Performance: Use predictive analytics to keep your gear running smoothly.
Predict Energy Demand: Machine learning helps you plan and cut costs.
Keep an Eye on Systems: Real-time monitoring with IoT and AI means fewer surprises.
Stop downtime Early: Predictive maintenance saves money and headaches.
Grow on Your Terms: Scalable solutions fit your needs now and later.
Hit Sustainability Targets: Track emissions and go greener.
Smarter Decisions: Get insights that actually help you act.
Save Money: Automate tasks and boost ROI.
Boosting Power Plant Profits with Data-Driven Intelligence
Intelligent algorithms analyze real-time sensor data from power generation equipment to predict maintenance needs and prevent costly breakdowns before they happen. Advanced analytics optimize fuel consumption, power output, and grid distribution by identifying inefficiencies and automatically adjusting operations. AI-powered forecasting helps match power generation with demand peaks, reducing waste while maximizing revenue through optimal pricing and resource allocation.
AI-Powered Predictive Maintenance Success Story
At a major combined cycle power plant in Texas, implementing AI-driven predictive maintenance transformed operations. The facility, generating 800MW of power, experienced 3-4 unexpected shutdowns annually, each costing approximately $1.2M in repairs and lost revenue. Their solution: deploying an AI system monitoring 10,000+ sensors across critical equipment.
The AI analyzed real-time data from turbines, generators, and auxiliary systems, establishing baseline performance patterns. Machine learning algorithms detected subtle deviations from normal operations, identifying potential failures weeks before traditional methods. The system particularly excelled at predicting turbine bearing issues and steam system anomalies through vibration analysis and thermal pattern recognition.
First-year results showed dramatic improvements:
- Unplanned downtime reduced by 85%
- Maintenance costs cut by $2.8M
- Overall equipment effectiveness improved from 82% to 94%
- Energy efficiency increased by 5%
- ROI achieved within 9 months
The same technology scaled across their facility portfolio, including cooling systems, substations, and distribution networks. The key to success was integrating the AI insights with existing maintenance workflows and training staff to effectively respond to predictive alerts.
This approach translates directly to other energy-intensive facilities. Data centers can predict HVAC failures, manufacturing plants can optimize production line energy use, and office buildings can automate climate control while preventing equipment failures. The key principle remains: converting sensor data into actionable insights prevents costly breakdowns while optimizing energy efficiency.
Data Science Drives E-Commerce Giant's Green Energy Success
A leading e-commerce company launched a pioneering renewable energy integration project across its Arizona data centers. The challenge was managing 70% of its energy needs through wind and solar while maintaining 99.99% uptime for critical operations.
Their data science team deployed an AI-powered energy management system that processes weather forecasts, historical performance data, and real-time grid conditions. The system predicts renewable energy availability 72 hours ahead with 94% accuracy, automatically adjusting workloads and storage systems to match energy patterns.
Key components
- Machine learning algorithms analyze weather patterns and energy generation data
- Bright grid integration balances on-site generation with grid power
- Automated load shifting moves compute tasks to times of peak renewable generation
- Battery storage systems optimized through predictive analytics
- Real-time monitoring and automated failover systems
First-year results
- 45% reduction in energy costs
- 60% decrease in carbon emissions
- Zero downtime from renewable energy variability
- $4.2M savings in operational costs
- 3.2-year ROI on infrastructure investment
This approach scales to any business size. Smaller companies can start with smart meters and rudimentary analytics to optimize energy usage patterns. Mid-sized businesses can integrate smaller renewable installations with battery storage, using predictive analytics to maximize renewable usage. The key is starting with good data collection and gradually building intelligence into energy management systems. The critical first step for companies considering similar initiatives is installing monitoring systems to establish baseline energy usage patterns. This data becomes the foundation for optimization strategies.
Your Competitive Edge in Industry 4.0
Companies leveraging Energy 4.0 technologies are transforming operations through real-time monitoring, predictive analytics, and AI-driven optimization, achieving up to 70% reductions in equipment downtime and 25-40% cuts in peak load costs.
Early adopters of data science in power generation report 30-45% reductions in energy costs, with manufacturers using AI-optimized systems cutting production costs by 15-20%. Data centers implementing smart cooling solutions have reduced bills by 40%, while retail chains deploying predictive HVAC analytics save $3M annually per 100 stores. Warehouses combining IoT sensors with machine learning typically see a 35% reduction in energy waste.
These improvements extend beyond direct savings. Companies gain enhanced brand value through demonstrated environmental leadership, improved ESG scores, and access to green financing. Their operations become more resilient against grid disruptions and energy price volatility. Most importantly, they already comply with emerging sustainability regulations like the EU's Green Deal, avoiding costly future retrofitting.
The competitive advantage is clear: businesses implementing data-driven energy solutions today build cost efficiencies that compound over time. As energy prices rise and regulations tighten, the gap between early adopters and laggards widens. For example, manufacturing facilities leveraging AI for energy optimization report reduced costs and improved product quality and production speeds—benefits that directly impact market competitiveness.
Implementation follows a proven path: start with comprehensive energy monitoring systems that establish usage baselines and identify immediate optimization opportunities. Gradually add intelligence through machine learning algorithms that predict maintenance needs, optimize load scheduling, and automate responses to changing conditions. This staged approach delivers quick wins while building internal expertise and funding further improvements through realized savings.
Critical success factors include integrating these systems with existing operations, training staff to act on AI-generated insights, and maintaining a mindset of continuous improvement. Leading companies create energy optimization teams that combine data science expertise with operational knowledge.
The sustainability impact resonates with stakeholders: customers increasingly prefer environmentally responsible brands, investors scrutinize energy efficiency metrics, and regulators reward proactive adoption of green technologies. Companies demonstrating leadership in energy optimization often secure preferential financing rates and gain priority access to renewable energy sources.
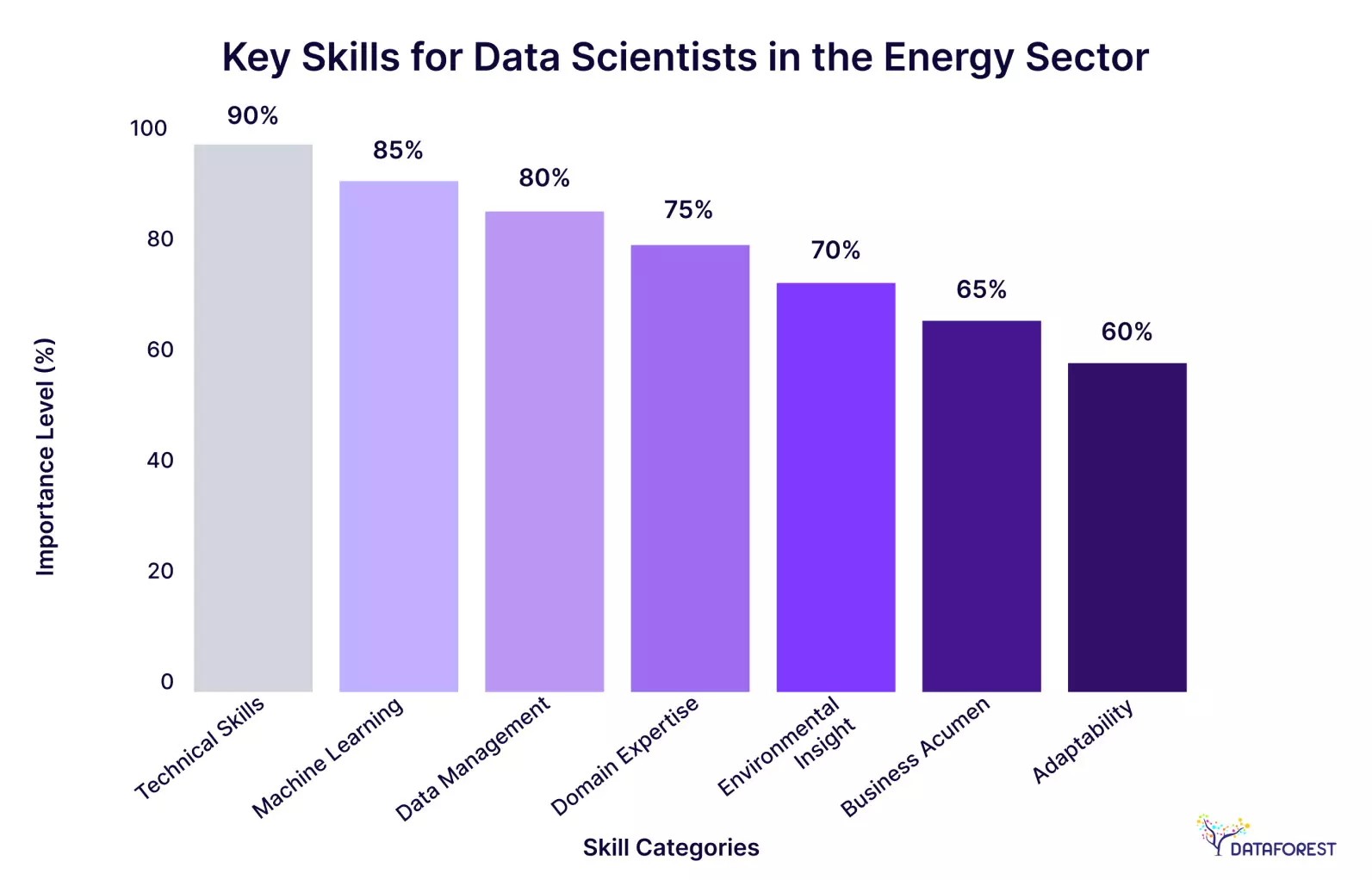
Get Started to Transform Your Energy Management
Step 1: Assess Your Current Energy Management System
Before diving into advanced solutions, it's essential to understand your current energy infrastructure. This step involves assessing how energy is produced, distributed, and consumed within your business. Identifying inefficiencies and gaps will help you determine where data science can make an impact.
How to Assess Your Energy Infrastructure
Audit Energy Sources and Usage: Start by mapping out where your energy comes from (e.g., grid, renewables, generators) and where it is used. Break this down by department, process, or location.
Monitor Performance: Install IoT sensors to track energy usage in real time. Analyze patterns to identify areas of high consumption and potential waste.
Evaluate Costs and ROI: Compare your energy bills and maintenance costs to industry benchmarks to pinpoint areas for improvement.
Identify Data Gaps: Determine if critical energy data is missing or siloed across systems, which can hinder optimization efforts.
Framework for Evaluation
Energy Demand: Is your energy consumption consistent or seasonal? Are peak times optimized?
Infrastructure Age: Are your systems modern or outdated? Older systems may require retrofitting for compatibility with smart tools.
Data Readiness: Have you already collected energy data, and is it stored in a format that can be analyzed?
Step 2: Leverage Data Science for Immediate Benefits
Once you’ve identified areas for improvement, the next step is to implement data science solutions to address them. The goal here is to focus on quick wins—actions that deliver results without requiring a massive upfront investment.
Quick Wins with Data Science
Predictive Maintenance: Use AI-powered algorithms to analyze equipment performance and predict failures before they happen. This reduces downtime and saves on repair costs.
Energy Load Optimization: Implement predictive analytics to balance energy loads during peak and off-peak hours, lowering costs and improving efficiency.
Anomaly Detection: Use machine learning to identify unusual energy consumption patterns, which could indicate leaks, faulty equipment, or energy theft.
Start Small, Scale Quickly
Pilot Projects: Begin with a small project, such as optimizing the energy use of a single facility. Use the results to refine your approach before scaling up.
Cloud-Based Tools: Platforms like AWS, Google Cloud, and Azure provide affordable, scalable solutions for small—and medium-sized businesses. Their pay-as-you-go models eliminate the need for large upfront investments.
Pre-Trained Models: To reduce implementation time, leverage pre-built AI models. Many tools come with ready-to-use features for energy management.
Step 3: Partner with Experts to Implement Scalable Solutions
Transforming energy management at scale requires expertise. While DIY approaches can yield quick wins, partnering with data science consultants or energy specialists can accelerate your transition to Energy 4.0 concept.
Benefits of Working with Experts
Customized Solutions: Consultants tailor strategies to your specific needs, ensuring optimal results.
Access to Advanced Tools: Experts often have access to cutting-edge technologies and platforms, which can be expensive or difficult to implement independently.
Faster Implementation: With experience in energy projects, consultants can deploy solutions more efficiently, saving time and resources.
Ongoing Support: Many partners offer continuous monitoring and optimization to ensure sustained benefits.
Finding the Right Partner
Experience: Look for firms with a proven track record in energy management and data science.
Industry Knowledge: Choose partners familiar with your sector’s unique challenges and requirements.
Scalability: Ensure they can scale solutions as your business grows.
Collaborating with experts speeds up implementation and reduces risks. By leveraging insights, you can avoid common pitfalls and ensure your energy management system is future-proof.
The High Costs of Delaying Technology Adoption
With its experience in data engineering, DATAFOREST believes that putting off adopting new technology can cost a business big time. Outdated systems mean clunky processes, more errors, and higher costs. Businesses that utilize innovative grid technology and operational intelligence gain a competitive edge by reducing energy waste and achieving sustainability targets. That’s a lot of missed opportunities to cut costs and boost efficiency.
But it’s not just about fixing what’s broken—it’s about staying ahead. Businesses using predictive analytics and AI are spotting trends, meeting customer needs faster, and out-innovating everyone else. The longer you wait, the more market share you lose to those already riding the tech wave.
In energy, retail, or fintech, jumping on scalable tools now means slashing expenses, going greener, and standing out from the crowd. Late adopters are stuck playing catch-up, dealing with stricter implementation and skyrocketing costs. Worst case, they risk fading into irrelevance.
Modern tech is easier to access and scale than ever. Waiting is risky and a surefire way to fall behind. Please complete the form, get started, and keep your business in the game.
FAQ
How can data science help my business reduce energy costs immediately?
Data science can optimize energy usage by analyzing consumption patterns, predicting peak demand, and identifying real-time inefficiencies. Quick wins include reducing waste, scheduling maintenance proactively, and balancing energy loads to cut costs instantly.
Can small and mid-sized companies benefit from Energy 4.0 solutions?
Scalable tools like cloud-based platforms and pre-built AI models make Energy 4.0 accessible, allowing smaller companies to optimize energy usage without large upfront investments.
What is the ROI of implementing data-driven energy solutions?
The ROI is typically fast. Within months, businesses often see reduced energy costs, lower downtime, and extended equipment life. Many companies report savings of up to 20% through smart energy management.
How do I integrate renewable energy into my operations without major disruptions?
Using IoT and AI-driven tools, businesses can seamlessly balance renewable energy sources with traditional ones. Smart microgrids and predictive analytics ensure reliability while integrating renewables smoothly into operations.
Is data science in energy only for large corporations, or can smaller businesses exploit it?
Smaller businesses can absolutely benefit by leveraging affordable, scalable technologies like IoT sensors and cloud-based analytics. These tools offer the same optimization and savings benefits at a fraction of the cost.