During a severe winter storm, a power utility company faced multiple failing transformers across their grid. It could threaten widespread outages for millions of residents. While traditional maintenance schedules suggested the transformers had years of life left, only the AI-powered predictive system detected subtle anomalies in performance data indicating imminent failures. Armed with the intelligence, the company proactively replaced the critical transformers days before record-breaking cold temperatures hit the region. The condition-based maintenance approach prevented what could have been life-threatening power outages during extreme weather conditions, saving both lives and millions in emergency repair costs. When later analyzed, the subtle pattern of transformer degradation would have been impossible to detect through conventional monitoring methods, making condition monitoring the only viable solution for averting this crisis. Schedule a call to complement reality with a profitable tech solution, ensuring equipment reliability and optimized maintenance planning.
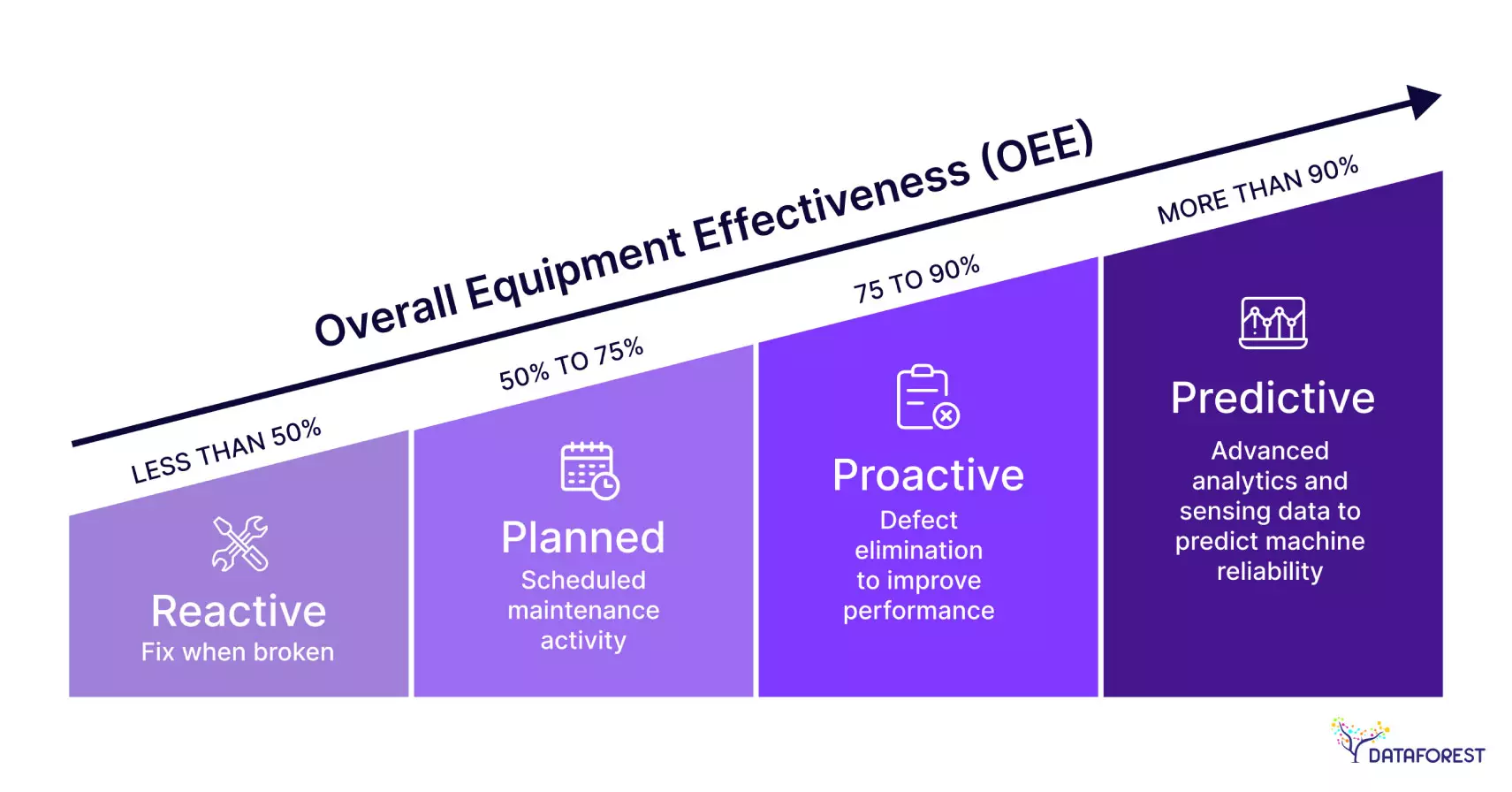
Transforming Utility Infrastructure Management
With equipment scattered across cities and countryside, keeping everything running smoothly is like juggling while walking a tightrope. IoT sensors keep tabs on everything from power transformers humming away in substations to water pumps working underground. These sensors feed data to smart systems that use AI and machine learning to spot trouble before it hits. It's getting a heads-up that your car's going to break down next week instead of being stranded on the highway.
Utility companies deal with infrastructure that's often older than most of their employees. Mix in crazy weather patterns (thanks, climate change), stricter regulations, and the pressure to keep costs down while keeping services up, and you've got yourself a perfect storm. Traditional "fix it when it breaks" or "check it every six months" approaches no longer cut it. Instead, modern reliability engineering and maintenance optimization strategies are leading the way.
The numbers tell a compelling story. Companies jumping on the predictive maintenance bandwagon are seeing downtime reduction by more than half. Equipment downtime decreased by more than half. And instead of replacing expensive gear every few years, they're squeezing out an extra 20-40% of life from their assets. For utility companies watching their budgets while trying to keep millions of customers happy, that's like finding money in your couch cushions - but on a massive scale.
Looking down the road, things get even more interesting. Predictive maintenance is becoming the backbone of truly smart utilities as IoT tech gets cheaper and AI gets smarter. It's preventing failures and creating utility networks that practically manage themselves. Combine this with renewable energy integration and smart grid tech, and you're looking at the future of utility management. And consider: we're just scratching the surface of what's possible.
AI-Powered Utility Asset Management
Predictive maintenance is a proactive equipment management strategy that uses real-time monitoring and data analytics to forecast failures, replacing reactive and scheduled maintenance approaches. The technology combines IoT sensors, machine learning algorithms, and advanced analytics platforms to continuously collect and analyze equipment performance data, including vibration patterns, temperature fluctuations, power consumption, and other critical parameters. The move to condition-based maintenance has transformed the utility industry by reducing operational costs by up to 40%, improving equipment efficiency, preventing service interruptions, and extending the asset lifecycle. It also enables utilities to move from crisis management to strategic maintenance workflow planning.
Predictive vs. Preventive Maintenance
Traditional preventive maintenance relies on fixed schedules and manufacturer recommendations to perform routine inspections and part replacements, regardless of actual equipment condition. This time-based approach often results in unnecessary maintenance of healthy equipment while missing developing issues between scheduled services.
Predictive maintenance uses real-time data and AI analytics to monitor equipment conditions. IoT sensors track performance metrics (vibration, temperature, and electrical signatures), and machine learning algorithms analyze the data to detect subtle degradation patterns and predict failures weeks or months in advance.
The key differences lie in timing and efficiency. While preventive maintenance might replace a transformer component every three years regardless of condition, predictive maintenance initiates repairs only when asset health data indicates an emerging problem. This targeted approach improves equipment diagnostics and ensures maintenance strategy success by reducing costs and preventing unexpected failures.
Key Technologies Driving Predictive Maintenance in Utility Services
IoT sensors continuously monitor equipment health. For example, Virginia Electric Power uses smart sensors to detect early signs of transformer deterioration, preventing potential failures.
AI and Machine Learning algorithms analyze this sensor data to identify patterns and predict potential failures. Pacific Gas & Electric employs ML models to forecast equipment failures by analyzing historical performance data alongside real-time sensor readings, reducing unplanned downtime by 30%.
Big Data platforms store and process the massive amounts of data generated. Duke Energy's data analytics system processes over 85 billion data points annually from their grid sensors, enabling precise maintenance scheduling.
These technologies work together in practical applications:
- Competent grid operators use IoT sensors and ML to predict transformer health
- Water utilities employ pressure sensors and AI to detect pipe leaks before they occur
- Gas companies utilize thermal sensors and predictive analytics to identify potential pipeline issues
- Power distribution companies combine weather data with grid sensor information to predict storm-related outages
Impact of Predictive Maintenance on Utility Reliability
Power plants using predictive analytics have reduced forced outages by up to 40%. The technology lets utilities monitor critical parameters like turbine vibration, transformer oil temperature, and equipment wear patterns. This data-driven approach helps optimize maintenance schedules, extend equipment life, and maintain a consistent power supply, improving grid reliability and customer satisfaction.
Predictive Maintenance Applications in Energy Infrastructure
This matrix outlines four major energy infrastructure types and their predictive maintenance frameworks. Each category (Power Plants, Power Grids, Wind Farms, and Solar Plants) is analyzed across four dimensions: monitoring parameters, technology implementation, operational benefits, and ROI metrics.
We can consider your case; just schedule a call.
Transforming Water and Gas Utilities Through Predictive Maintenance
In water utilities, smart sensors monitor pipe pressure, water quality, and flow rates, enabling early detection of leaks and potential contamination. Advanced analytics can predict pipe failures up to weeks in advance, reducing water loss by 25-30% and preventing costly emergency repairs.
For gas utilities, the technology focuses on pipeline integrity and safety. IoT sensors monitor gas pressure, temperature, and composition, while AI algorithms analyze this data to detect potential leaks or equipment failures. Companies like Southern California Gas have reported a 35% reduction in emergency repairs after implementing predictive maintenance systems.
Both sectors benefit from enhanced asset management. Water utilities use ML algorithms to optimize pump operations and predict equipment failures. Gas utilities employ thermal imaging and acoustic sensors to monitor pipeline conditions while improving safety metrics.
These systems enhance public safety by preventing major incidents like water main breaks or gas leaks, leading to improved customer satisfaction and regulatory compliance. The technology has proven particularly valuable in aging infrastructure management, helping utilities prioritize replacement schedules based on data-driven risk assessments.
The Mechanics of Predictive Maintenance in Utilities
Predictive maintenance is a continuous data collection, analysis, and action cycle. IoT sensors installed on utility equipment (transformers, pipelines, pumps) constantly monitor key performance indicators like temperature, vibration, and power consumption.
Data Flow Architecture
The data journey in predictive maintenance starts at the equipment level with a network of IoT sensors capturing multiple parameters. These sensors continuously monitor vibration patterns, thermal signatures, electrical loads, pressure levels, and acoustic emissions from critical utility assets like transformers, turbines, and distribution networks.
This raw sensor data streams through secure gateways using industrial protocols (like MQTT or OPC-UA) to edge computing devices, which perform initial data filtering and preprocessing. The edge devices clean the data, remove noise, and detect preliminary anomalies before transmitting refined data to central processing systems.
Sophisticated analytics engines process data in the cloud or on-premises servers through multiple layers. First, real-time analytics compare current readings against established baselines. Simultaneously, machine learning models analyze historical patterns to identify subtle deviations that might indicate developing issues. AI algorithms then correlate these findings with maintenance histories and environmental data to predict potential failure scenarios.
The system uses advanced pattern recognition to distinguish between normal operational variations and genuine problem indicators. When potential issues are detected, the platform generates automated alerts with detailed diagnostic information, probability assessments, and recommended actions, all delivered to maintenance teams through mobile apps or control center dashboards.
Predictive Analytics for Utility Equipment Failure
Machine learning in utility predictive maintenance employs multiple algorithms to achieve accurate failure predictions. Time series analysis forms the foundation, using LSTM (Long Short-Term Memory) neural networks to process sequential sensor data and identify temporal patterns in equipment behavior.
Regression models, particularly Random Forests and Gradient Boosting Machines (like XGBoost), estimate components' Remaining Useful Life (RUL) by analyzing historical failure data alongside current performance metrics. For example, a Random Forest might analyze transformer oil temperature trends, load patterns, and age to predict potential failure within specific time windows.
Anomaly detection leverages algorithms like Isolation Forests and One-Class SVMs (Support Vector Machines) to identify unusual equipment behavior. These techniques create a "normal" operation baseline and flag deviations, such as sudden changes in turbine vibration patterns or unexpected power consumption spikes.
Deep neural networks, specifically Convolutional Neural Networks (CNNs), process complex sensor data patterns. For instance, CNNs can analyze acoustic signatures from gas pipelines to detect developing leaks or structural weaknesses. Ensemble methods, weighted by historical accuracy, combine these predictions to provide final failure probability assessments and recommended maintenance timeframes.
Critical Challenges in Utility Predictive Maintenance
Utility companies face unique challenges due to their geographically dispersed infrastructure networks, where installing and maintaining reliable sensor coverage across thousands of miles of power lines, pipelines, and remote substations requires significant investment and innovative connectivity solutions. The diverse nature of utility assets, from decades-old legacy equipment to modern innovative grid components, creates complexity in data standardization and requires sophisticated ML models capable of handling both historical maintenance records and modern IoT sensor data. The critical nature of utility services means predictive maintenance systems must achieve high accuracy rates while processing massive amounts of real-time data, as false positives can trigger costly, unnecessary maintenance. At the same time, missed predictions can lead to service interruptions affecting millions of customers.
We know how to handle Big Data: book a call, and you will know it too.
Implementing Predictive Maintenance in Utility Operations
- Start with a pilot program on critical assets rather than attempting a company-wide rollout. This allows teams to validate the approach, demonstrate ROI, and build internal expertise before scaling up.
- Establish a robust data collection infrastructure with redundant sensors and reliable connectivity. Consider edge computing solutions for remote locations where network connectivity might be unreliable. Work with equipment manufacturers to ensure sensor compatibility and proper installation procedures.
- Cultural resistance often proves more challenging than technical issues. Engage maintenance teams early in implementation, incorporating their expertise into system design and alert thresholds. Provide comprehensive training that emphasizes how predictive tools complement rather than replace human expertise.
- Implement robust security protocols and work closely with IT teams to address cybersecurity concerns from the start. Consider a hybrid cloud approach that isolates critical control systems while enabling advanced analytics capabilities.
- Focus initial budget implementations on assets where failures have the highest cost impact. Document early wins carefully – demonstrated success with high-value assets makes it easier to justify broader implementation.
Strategic Advantages of Predictive Maintenance in Utility Operations
Reduced Operational Costs: Targeted maintenance based on actual equipment condition cuts unnecessary repairs by 20-40%, optimizes spare parts inventory, and reduces emergency maintenance expenses through early issue detection and planned interventions.
Extended Asset Lifespan: Real-time monitoring and early intervention add 20-40% to equipment life expectancy by preventing cumulative damage and maintaining optimal operating conditions for critical infrastructure components.
Enhanced Service Reliability: AI-driven failure prediction dramatically reduces unplanned outages and service interruptions, improving customer satisfaction and helping utilities meet strict regulatory performance standards.
Optimized Workforce Management: Data-driven maintenance scheduling enables better resource allocation, reduces overtime costs, and allows skilled technicians to focus on truly critical tasks rather than routine inspections.
Regulatory Compliance: Comprehensive equipment monitoring and maintenance documentation helps utilities meet increasingly stringent regulatory requirements while providing detailed audit trails of asset management practices.
Energy Efficiency Improvements: Continuous performance monitoring identifies efficiency losses early, enabling adjustments that reduce energy consumption and operational costs across the network.
Safety Enhancement: Early detection of potential equipment failures reduces the risk of catastrophic breakdowns, protecting both utility workers and the public from dangerous situations.
Environmental Impact Reduction: Proactive maintenance minimizes the risk of environmental incidents like oil leaks or gas emissions, while optimal equipment operation reduces the overall carbon footprint.
Investment Planning Support: Detailed equipment performance data and degradation patterns enable more accurate capital planning and help justify infrastructure investments to regulators.
Smart Grid Integration: Predictive maintenance systems complement innovative grid technologies, providing crucial data for network optimization and enabling efficient integration of renewable energy sources.
Customer Experience Improvement: Fewer service interruptions, faster issue resolution, and the ability to proactively communicate maintenance schedules enhance customer satisfaction and trust.
Predictive Maintenance Across Utility Sectors
In power generation facilities, predictive maintenance focuses on critical equipment that can cause catastrophic failures. Power plants employ vibration analysis systems on turbines and generators, using advanced neural networks to detect changes in operational patterns. Thermal imaging and acoustic sensors monitor transformer health to analyze oil temperature patterns and electrical signatures. These systems process real-time data, comparing current performance against historical baselines to identify degradation trends.
Wind farms present unique challenges due to their remote locations and exposure to harsh weather conditions. Here, predictive maintenance combines multiple data streams—vibration sensors in gearboxes and bearings and stress sensors in turbine blades. Machine learning algorithms analyze this data alongside weather patterns. Drone inspections complement sensor data, providing visual assessments of blade condition and structural integrity.
Solar installations rely heavily on performance monitoring systems that track individual panel output and inverter efficiency. Predictive maintenance in this sector focuses on detecting degradation patterns, identifying underperforming components, and predicting cleaning needs based on environmental data. Thermal imaging drones help identify hot spots that indicate failing cells or connection issues, while weather data integration helps optimize maintenance timing.
Water utility networks focus on leak detection and water quality maintenance. Advanced acoustic sensors monitor pipeline networks, while AI algorithms analyze flow rates, pressure data, and water quality parameters to predict potential issues. Machine learning models process this data alongside historical repair records and environmental factors to identify high-risk segments requiring preventive intervention.
In water treatment plants, predictive maintenance systems monitor critical equipment like pumps, filters, and chemical dosing systems. Real-time analysis of operational parameters helps optimize chemical usage and predict equipment failures before they affect water quality. AI models analyze patterns in water quality data to predict treatment needs and potential equipment stress points.
Gas pipeline networks employ specialized sensor systems focusing on pressure monitoring and leak detection. Fiber optic cables along pipelines provide continuous temperature and strain measurements while advanced analytics process this data to detect potential leaks or structural issues. Machine learning algorithms analyze flow patterns and pressure data to optimize network operation and predict potential failure points.

The Future of Predictive Maintenance in Utility Services
AI and ML in predictive maintenance are advancing toward more sophisticated applications. Deep learning algorithms will enable real-time anomaly detection with 99% accuracy, while digital twins will provide precise equipment behavior simulation. Edge computing will allow instant data processing, reducing response times from hours to seconds.
Natural Language Processing (NLP) will automatically transform maintenance reports into actionable insights. Quantum computing integration will enhance complex pattern recognition across vast datasets. Advanced AI will enable self-healing systems that can automatically adjust operations to prevent failures. These technologies will reduce maintenance costs by 50% and extend asset life by 30% while achieving near-zero unplanned downtime.
Future Trends in Utility Industry Technology
The utility industry is rapidly embracing autonomous systems for infrastructure management. Self-navigating drones will conduct 80% of aerial inspections, using AI-powered imaging to detect real-time issues. Robotic systems will perform underwater pipe inspections and automated repairs without service interruption.
Remote monitoring will evolve with 5G and satellite connectivity from centralized control rooms for grid management. Digital twin technology will provide virtual replicas of entire utility networks, allowing operators to simulate and optimize operations instantly.
Smart sensors and IoT devices will create a self-diagnosing infrastructure network, while autonomous maintenance robots will handle routine tasks, reducing human intervention by 70% and improving worker safety by 85%.
Predictive Maintenance in Smart Cities
Predictive maintenance will form the backbone of smart city infrastructure management. Integrated sensors across power grids, water systems, and transportation networks will create a unified maintenance ecosystem. AI algorithms will coordinate maintenance schedules across multiple city systems.
Smart streetlights will self-diagnose issues, while underground sensors will detect infrastructure problems before they surface. Traffic systems will automatically adjust based on wear patterns and usage data. Connected waste management systems will optimize collection routes and maintenance schedules.
This integrated approach will reduce city maintenance costs by 40%, improve service reliability by 60%, and enhance urban resilience through proactive infrastructure management.
Digital Integration in Utility Services
Predictive maintenance is becoming seamlessly integrated with broader digital transformation initiatives. Cloud-based platforms now connect maintenance systems with customer service portals, workforce management, and enterprise resource planning. The integration makes real-time coordination between maintenance predictions and operational decisions.
Smart meters feed data directly into predictive algorithms, while blockchain technology ensures data security and transparent maintenance records. Mobile workforce solutions automatically dispatch crews based on AI predictions. Customer apps provide real-time updates on maintenance activities and service status.
This digital ecosystem reduces response times by 65%, improves first-time fix rates by 40%, and enhances customer satisfaction scores by 35% while optimizing resource allocation across all utility operations.
Technology Partnership Strategy in Predictive Maintenance
Utilities should prioritize partnerships with technology specialists to implement predictive maintenance systems. Integrating IoT sensors, AI algorithms, and existing infrastructure requires specialized expertise that most utilities don't possess internally.
Technology partners like DATAFOREST bring proven implementation experience, ready-to-deploy solutions, and innovation capabilities. They offer pre-trained AI models, established cybersecurity protocols, and scalable cloud infrastructure solutions. The partnership reduces implementation risks, accelerates deployment, and ensures solution reliability.
However, utilities should maintain internal teams for day-to-day operations and maintenance while leveraging partners for advanced technical aspects. This hybrid approach gradually allows utilities to build internal capabilities while benefiting from partner expertise. Success stories like American Water's partnership with IBM demonstrate how this model can reduce implementation time by 50% and achieve ROI within 18 months.
Please complete the form to select the partner with utility industry experience, proven solutions, and strong integration capabilities.
FAQ
What are the challenges of implementing AI-driven predictive maintenance solutions in legacy utility systems?
Legacy systems often lack the necessary infrastructure, such as IoT sensors or integration capabilities, to support AI, making implementation complex and costly. Outdated equipment and employee resistance to change can also slow down the adoption process.
How can predictive maintenance improve energy generation reliability and reduce unplanned outages?
Predictive maintenance identifies potential equipment failures before they occur, allowing timely interventions and minimizing downtime. Ensuring key assets operate efficiently enhances system reliability and prevents costly unplanned outages.
What are the most effective machine learning algorithms for predictive maintenance in utility services?
Algorithms like Random Forests, Gradient-Boosting Machines, and Neural Networks excel at analyzing time series data and detecting anomalies in equipment behavior. These models are particularly effective at identifying subtle patterns and accurately predicting failures.
Can predictive maintenance solutions help utility companies scale their operations without increasing overhead costs?
Predictive maintenance automates monitoring and analysis, reducing the need for frequent manual inspections and repairs. This allows companies to manage more assets efficiently while lowering operational costs and extending asset lifespans.
How can predictive maintenance optimize the performance of renewable energy sources (e.g., solar, wind) in utility services?
Predictive maintenance detects issues like wear or inefficiencies early by continuously monitoring components like solar panels or wind turbines. This ensures optimal energy production and prevents significant downtime in renewable energy systems.
What role does real-time data analysis play in predictive maintenance for utilities, and how does it enhance decision-making?
Real-time data analysis provides instant insights into asset performance, enabling immediate responses to potential issues. This improves decision-making by reducing reaction times and prioritizing maintenance activities effectively.
How can predictive maintenance solutions be customized for specific utility sectors (e.g., water, energy, gas)?
Each sector has unique operational requirements, such as pressure monitoring in water systems or thermal analysis in gas pipelines. Customization involves tailoring IoT sensors, analytics platforms, and machine learning models to address these specific needs.